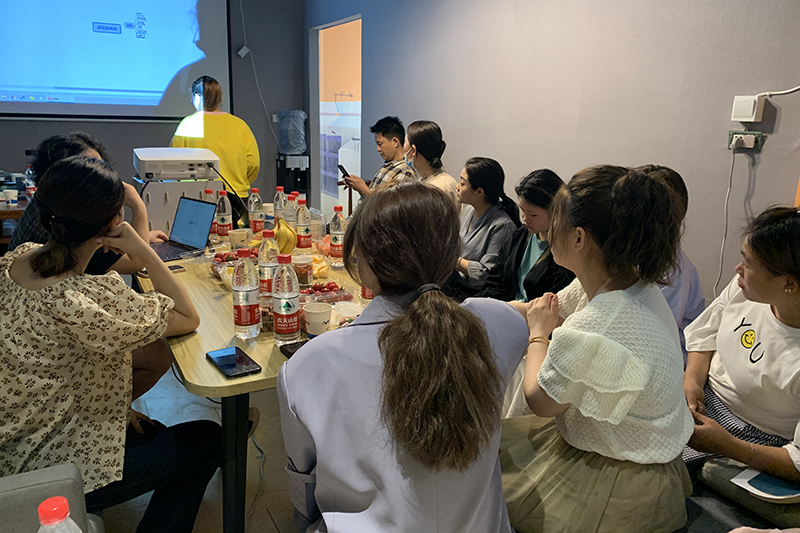
At the beginning, our business manager's job was to inspect goods for foreign brands. After 3 years of documentary experience and quality inspection experience, we have a very familiar mastery of foreign trade orders, and also know the requirements and popular trends of each country. Since then, there are more and more brand buyers, and we have done RI one after another. TZ, Ferrari, Lipton, Claire’s, Disney, Walgreen, Costa, Vinga, Unilever, Buc-ees, Netflix, and much more.. .
Later, we gradually began to build workshops and management according to the needs of customers.
Our difference is that we only say what we are sure of doing. For example, when trying to do RPET, many large factories refuse many brands to try because they feel troublesome, because RPET's abrasives are actually different from our usual AS and TRITAN abrasives. Yes, the flow speed is different, and the pressure and moulding speed of the machine are different, which determines that we need to do hundreds of tests, and then eliminate all kinds of problems that affect good products one by one. After the customer has always trusted and given us enough time to give us confidence in development. Finally, the brand of Lipton, the first order, was shipped. Although the scrap rate swallowed up the profits, it still did not give up. After 1 month, 2 months, 5 months, 1 year and 2 years, today is the fourth year for us to do RPET. We used robot fully automatic scratch-free equipment to reduce injection moulding to blow bottles. Because the plastic cup itself is prone to hang up, we insist on reducing the friction from the machine to the packaging line as much as possible to ensure that it is so crystal clear as the new machine comes out. This is the truth. Our RPET and glass are put together, and the brightness is brighter and more transparent. Brands are right. There is also more and more confidence.
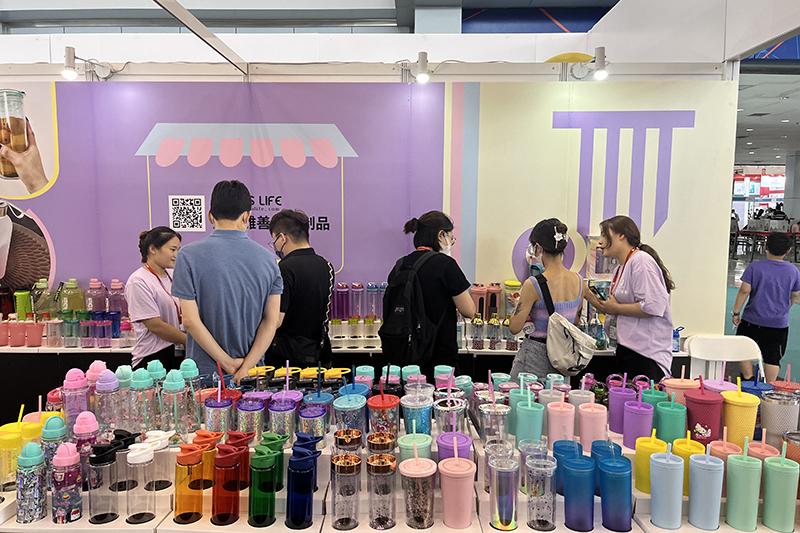

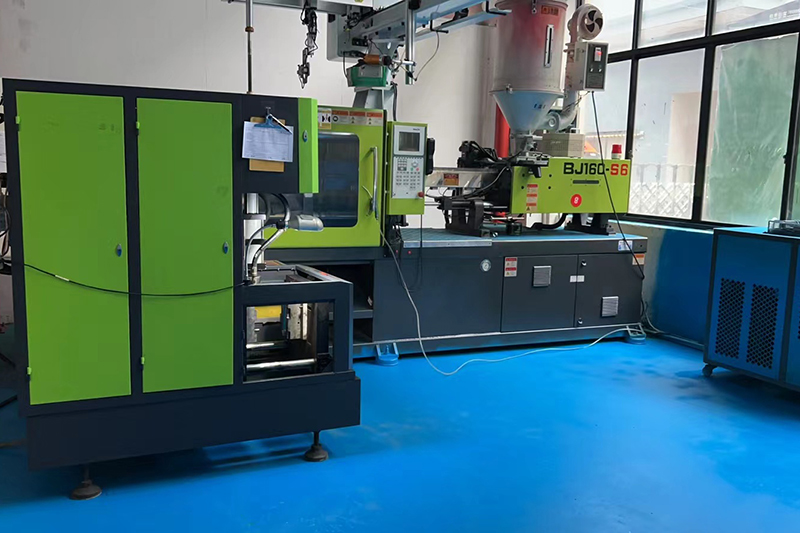
Our management is the evolution of helping employees build personal abilities, the evolution of knowledge, and the evolution of principles. Because of their low culture, the acceptance of knowledge by front-line employees is actually uneven, so we may need to slowly contact the establishment of simple principles for training employees, such as which level is acceptable So, which level is not, instead of relying on the instructions of our superiors, we hope that each of our Yashan factory has a common principle, so that our strength can resist greater challenges.
Post time: Nov-01-2022